|
|
|
CASE STUDY |

Europe's premier drainage manufacturer
more>>
|
|
|
Resource Plastics proved to be an innovative, professional and reliable partner. |
|
Road Signage Supplier
Client Name |
|
Road Signage Supplier |
Brief Description |
|
Innovative design and production sourcing of road signs in High Density polyethylene (HDPE). |
Date |
|
2006 |
Location |
|
UK |
Type |
|
Research, Design, Tool and Manufacturer sourcing |
Size |
|
|
Value |
|
|
Overview |
|
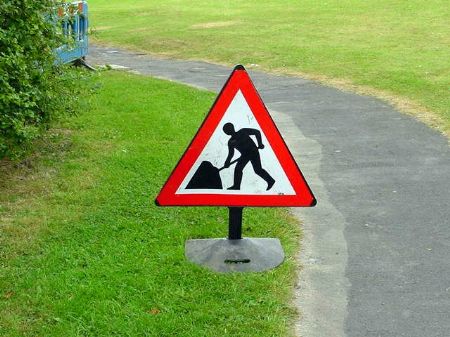
Background
Temporary road signs for road works and construction have been traditionally manufactured from steel which is a heavy, corrosive, energy consuming material. It also gives a potential for sparks when knocked over and could provide a serious hazard in gas main applications. Recent developments have been the introduction of Plastic (PVC) signs which go some way to reducing the weight and minimising the use of metal in the construction. The main drawback is that the signs are fabricated from several pieces of PVC and use metal studs to fasten the pieces together. PVC is also an unpopular material due to the Lead content (Pb) in the polymer and tends to embrittle in cold weather.
The Brief
We were asked to take a look at the current materials and manufacturing techniques available and to design a new style of sign that would,
1. Have reduced weight to save material, energy used in transport and increase the quantity able to be shipped by small commercial vehicles
2. Have no assembly requirement, a one piece sign.
3. Be completely recyclable.
4. Have good impact resistance and excellent cold weather performance (not get brittle)
5. Be manufactured from lead free material.
6. Have no metal components
7. Be user friendly for the construction worker.
8. Be quick and easy to assemble
9. Meet the size and design legislation specified
10. Be cost effective
11. Have good stability in cross winds and vehicle slip-streams
12. Be robust and long lasting.
The Design
The size and shape of the signs were dictated by the requirements of the legislation.
The improvements were brought about by re specifying the material to a lead-free polymer, well tried and tested in pipeline applications to low temeratures and which has a 30% lower (approx) specific gravity than PVC to provide a lightweight but robust structure yet is stonger than PVC with regard to impact and is stabilised against ultra violet light deterioration.
The manufacturing technique chosen was injection moulding. This allowed a one piece construction without the need for assembly thereby removing the need for metal fasteners. The design included an integral handle grip to aid the assembly process on site and structural bracing in the clients corporate identity (A)
Because the sign is one piece the product can be easily recycled at end of its useful lifetime and the polymer recovered used in packaging or similar applications. The material specification is identified by the recycling logo embossed on the sign itself to make recycling easier.
The sign was designed and drawn (modelled) using latest CAD techniques to ensure an efficient design for manufacturing and an aesthetically pleasing product which met the legislation applicable. The product is self coloured so there is no need for painting or finishing processes.
The sign fits into a heavy,recycled plastic base to give a low centre of gravity and provide stability on exposed roads, motorways or construction sites with continual traffic movement giving rise to extreme slip stream conditions. The base is able to be lighter than traditional designs due to the additional stability provided by the two out-rigger legs at the rear of the moulding. the surface area used as a footprint is no larger than existing bases but it is lighter and better able to stack, making it more cost efficient to transport in small vehicles. The base is made from completely recycled material (as are all the others)
Manufacturing
We researched potential suppliers on a global basis on the ability to produce such a large moulding to the exacting quality required in the polymer selected. Precision toolmaking allied to modern manufacturing techniques, quality assurance and good communication between manufacturer and customer were essential elements in creating the supply partnership.Resource Plastics selected the toolmaker and the manufacturer on behalf of the customer, negotiated price and project deadlines and managed the development and sampling stages of the project. When first-off samples were available, We undertook the measuring, testing and approval stages prior to bulk production. When all development issues were resolved we also set up the logistics to deliver good product to the customer on a "right first time" basis. |
|
Back
|
|
|
|
|
|
|